
Innovation and Success Fueled Additive Manufacturing in 2020
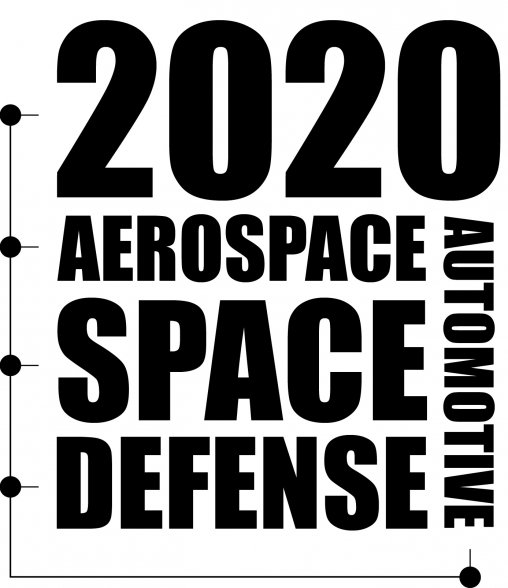
Elementum 3D helped early AM adopters overcome materials challenges
2020 was a big year for additive manufacturing (AM), with several key innovations and successes across a range of industries.
Any time a technology or industry pushes boundaries, there’s risk, but having the AM community closely connected, creates an ecosystem that helps mitigate risk.
In 2020, AM saw greater interest from aerospace, space, automotive, and defense manufacturers to engage with AM companies that complement their respective technologies and objectives.
Elementum 3D’s patented technology and materials development expertise support the AM ecosystem in overcoming one of its biggest challenges: … FULL STORY

Elementum 3D’s aluminum 7050 alloy awarded first ever Gold Medal at US Air Force’s Advanced Manufacturing Olympics
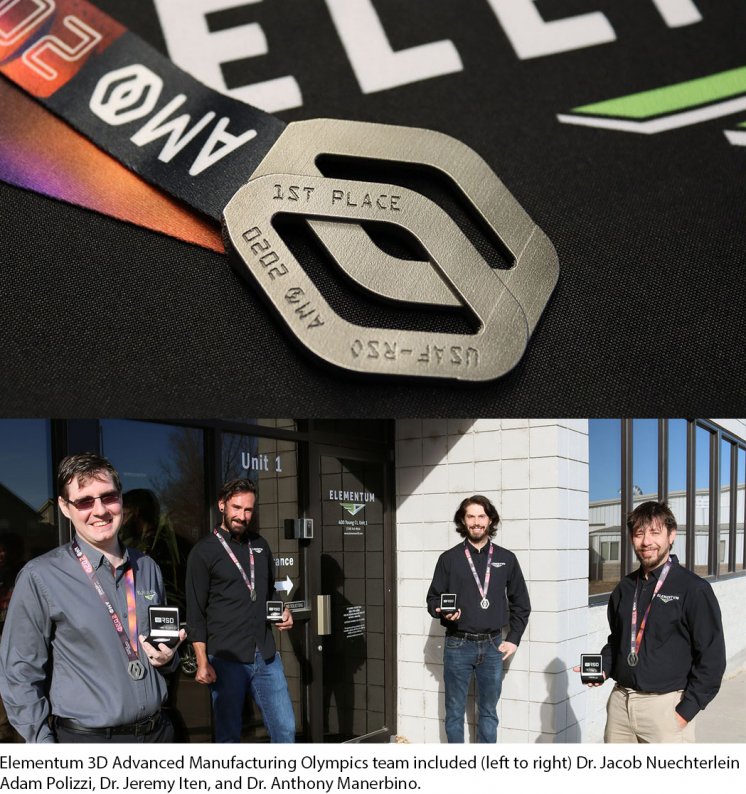
On October 23, 2020, the U.S. Air Force’s inaugural Advanced Manufacturing Olympics (AMO) Technical Challenges winners were announced. Elementum 3D’s A7050-RAM2 aluminum alloy was selected as the event’s first-ever “Material Hurdles” challenge Gold Medalist!
The eight other challenge finalist materials along with our A7050-RAM powder were evaluated on their ability to solve some of the U.S. Air Force’s most significant lightweight high-strength materials sustainment issues. The Material Hurdles Challenge was judged by 25 subject matter experts from academia, the U.S. Military (Air Force, Army, and Navy), the Federal Aviation Administration, Ford, Amazon, and aerospace and defense companies.
“We are honored to have our commercially available high-strength A7050-RAM2 aluminum alloy selected as the AM material to best meet the USAF’s challenge goal of demonstrating advances in AM aluminum material properties to address sustainment of traditionally manufactured 7075 and 7050 aluminum parts,” said Dr. Jacob Nuechterlein, President and founder of Elementum 3D.
The USAF is working to adopt additively manufactured aluminums because of their potential for rapid on-demand production of high-strength sustainment parts. Accomplishing this goal also facilitates reducing of component weights and reduced raw material requirements due to improved buy-to-fly ratios. Elementum 3D’s printable A7050-RAM2 feedstock supports these goals by enabling efficient 3D printing of components out of a lightweight high-strength aluminum material that also offers excellent fatigue life and stress corrosion cracking resistance.
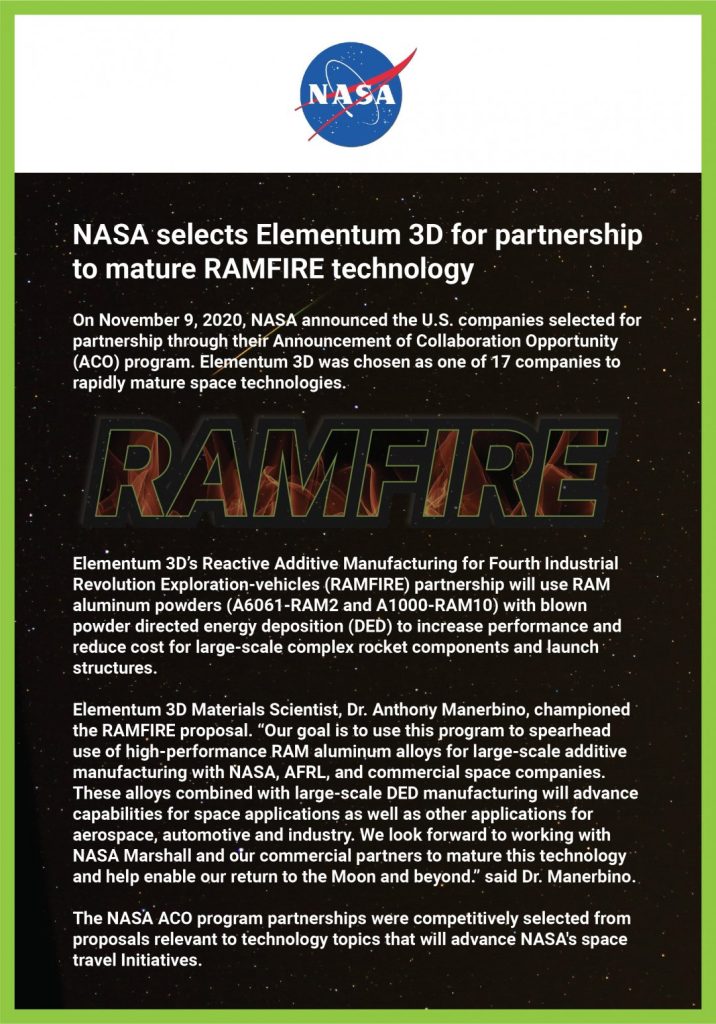
Elementum 3D’s copper alloy (GRCop-42) development is in its final countdown for approval to rocket into space.
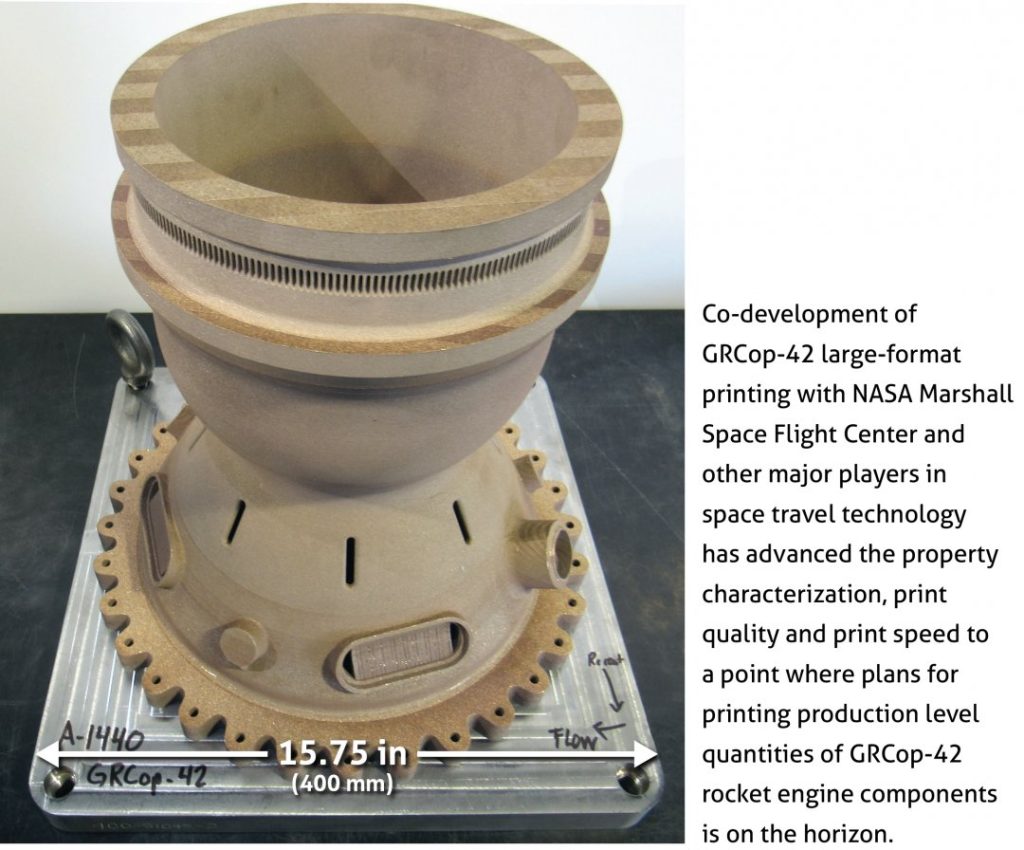
Materials data is the key to advancing metal additive manufacturing
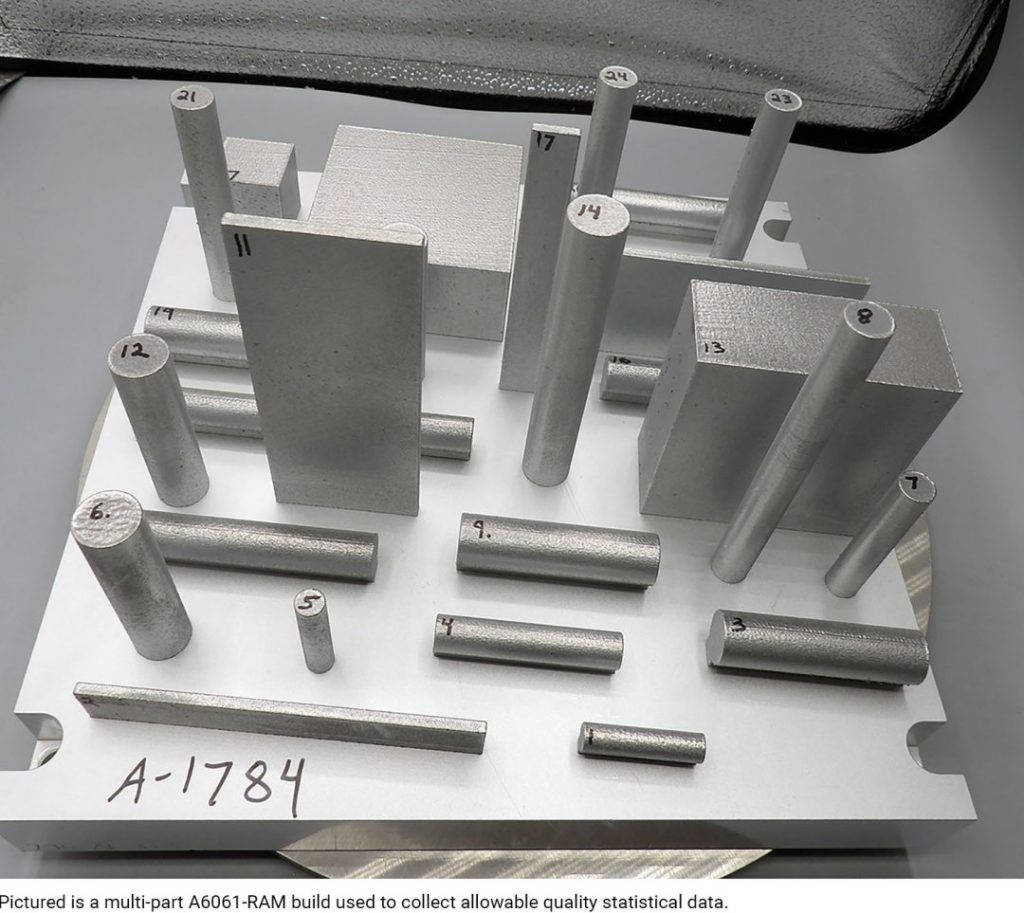
Elementum 3D recognizes the importance of statistical test data and is actively working to collect design-allowable quality statistical data for our materials. We have developed multi-part builds comprising a variety of test specimen types that are being printed by contract manufacturer partners and Elementum 3D in house. This methodology enables test specimen production across multiple feedstock lots and printers for testing at certified test labs. The extensive data generated by this process will be comparable to MMPDS data and can be used for component design and to facilitate part qualification. Elementum 3D expects to have statistical data across a range of properties comparable to S-basis data for our A6061-RAM2 material by early 2021 with other materials also in progress.
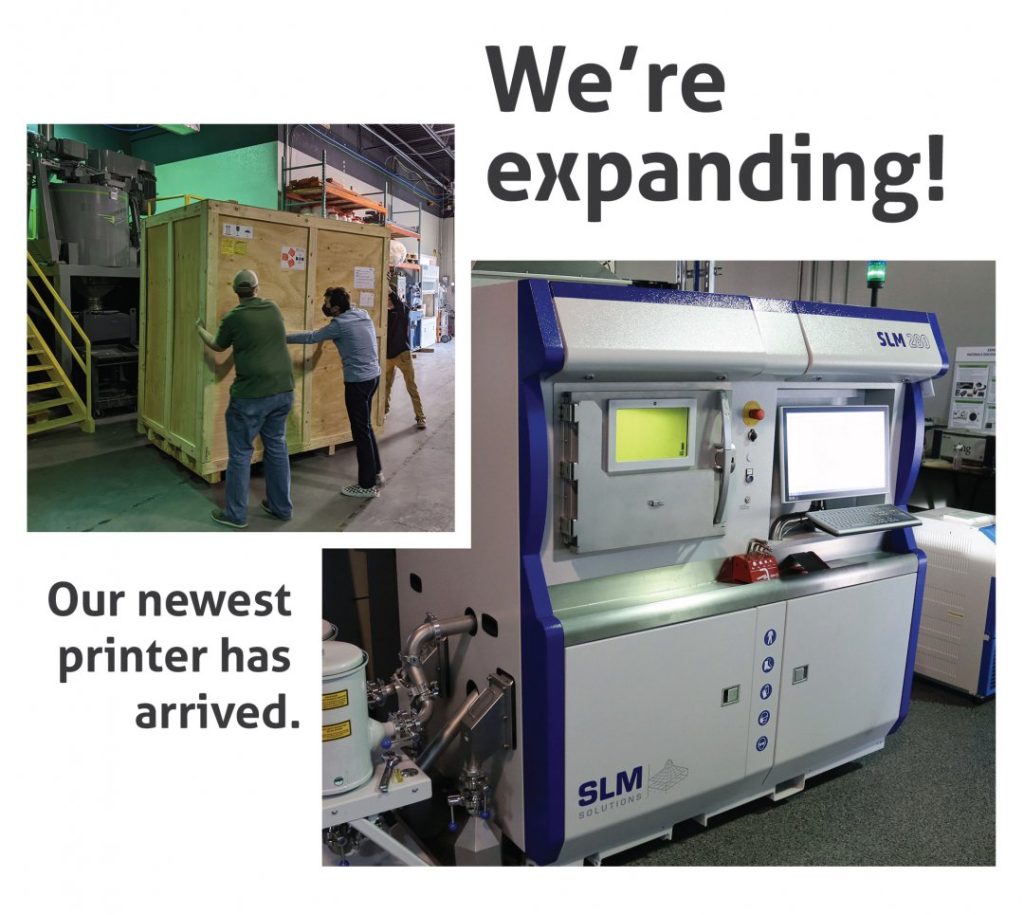

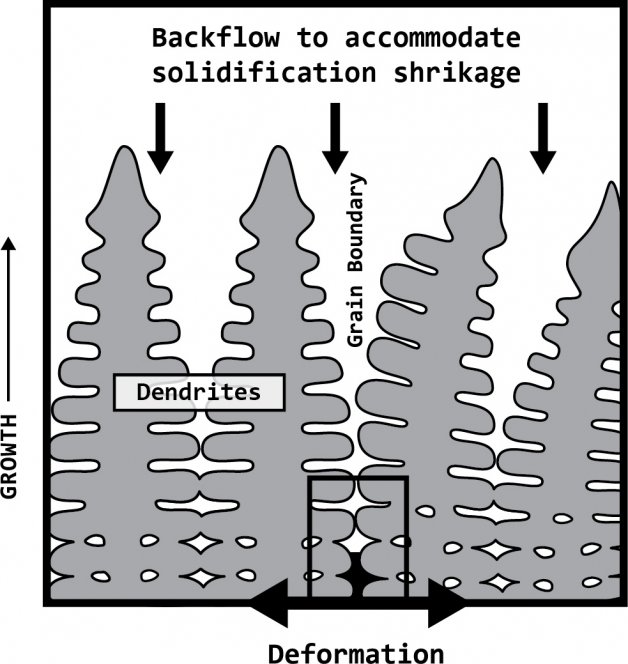
Understanding nucleation in AM alloys
In metallurgy, there’s a seemingly simple concept but ultimately complex process that metals undergo during a liquid-solid phase change; also termed solidification or freezing. This process refers to the nucleation and growth of the crystalline lattice grains that make up the solid structure. Many factors affect this phenomenon which define a metal’s physical and mechanical properties.
Solidification
Solidification can incur extensive supercooling, which will alter the way that the metal nucleates grains. Two types of grain nucleation can occur during solidification: homogeneous nucleation and heterogeneous nucleation. Both types of nucleation are governed by the thermodynamic quantity, Gibbs free energy, which defines a nuclei’s favorability to grow and form the crystalline lattice grains that make up the metal’s microstructure. FULL STORY

Employee update
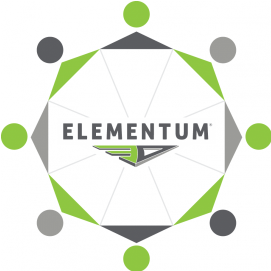
Q4 2020 NEW HIRES
Alex Janzen – Account Manager, Applications Engineer
Taylor Clevenger – Account Manager

- How to Integrate Additive Manufacturing Into Your Organization
- SLM Solutions builds prototype electric-drive housing for Porsche with its new NXG XII 600
- NASA Awards Relativity Space a Venture Class Launch Services Demonstration 2 Contract
- GM opens Additive Industrialization Center, 3D prints parts for Cadillac and Corvette Racing
- BMW targets industrial-scale additive manufacturing
- 3D Printed Electric Motor Components Drive Latest Additive Manufacturing Investment
- Army ponders 3D printed parts for its Black Hawk
- Air Force Searching for Savvier Sustainment
- 2020 NASA Announcement of Collaboration Opportunity (ACO) Selections
- NASA to “RAMPT up” Artemis program by DED 3D printing SLS rocket engine nozzles
- Leading the way: Baker Hughes on its deployment of 3D printing in oil & gas
- Japanese additive manufacturing is rising
- A route for avoiding defects during additive manufacturing
- Teach Engineers to Understand the Business Case
- Slow and Steady Wins the 3D Printing Race