
REM Surface Engineering – The surface finish experts
REM Surface Engineering and Elementum 3D first crossed paths at Rapid+TCT in 2018.
Justin Michaud, President and CEO of REM, attended a talk given by Jacob Nuechterlein, Founder and President of Elementum 3D. Jacob was presenting on the novel approach to additive materials the company was developing. While this was an interesting subject to Justin, what really caught his attention was how well Jacob knew his material — so well that when the A/V system cut out, he just kept going. Describing the slides his audience would see had the screen continued working, Jacob carried on with his presentation, with only his words and his knowledge keeping the audience captivated. Justin was impressed by both the technology and the man behind it, and an early alliance was formed.
REM Surface Engineering has been in the metals industry for 57 years. One of the secrets to REM’s success has perhaps been their adaptability to the changing needs of the industry they serve. When Justin first encountered metal in additive manufacturing (AM) he knew he needed to learn more about this developing field and how REM’s technology could impact this. He quickly discovered that metals produced in AM are a completely different animal than cast/wrought products. Working with various aerospace industry partners and NASA Marshall Space Flight Center (MSFC), REM began learning how their surface finish improvements could be tailored to suit the needs of the AM industry.
Elementum 3D is, of course, a much younger company, formed in 2014 as an AM materials R&D company. The primary focus of Elementum 3D’s work is developing powder feedstocks with the goal of expanding the library of printable alloys available in the industry. A6061 — one of the most widely used aluminum grades in traditional manufacturing but known to crack extensively in AM — was an early target of Elementum 3D’s efforts
Justin reviewed several materials in the early stages of research and Elementum 3D’s aluminum alloy A6061-RAM2 was selected to be the subject of REM’s first Air Force Phase 1 SBIR proposal. REM had experienced issues with L-PBF AlSi10Mg in the form of sub-surface porosity which limited the achievable surface finish and mechanical performance of printed parts. Though A6061-RAM2 has an excellent as-built surface finish and low porosity on its own, REM developed a process to further optimize the finish of this material, helping to maximize its material properties. NASA Jet Propulsion Laboratory (JPL) subsequently adopted A6061-RAM2 as a primary material for L-PBF use and implemented REM’s developed surface finishing process. Through REM’s work with NASA JPL, A6061-RAM2 materials are now being evaluated for use in spacecraft.
To move into the AM market, REM had to adapt to new standards. Justin knew that REM’s technology had to change to meet this need, and through experimentation developed new process technologies capable of removing 0.020” (500 µm) or more in a single process to address the more significant surface roughness as well as the near surface defects that are present on AM components. This development was a significant departure from REM’s standard process technology for traditionally manufacturing components which typically only requires 0.0001 – 0.0004” (2.5 – 10 µm) to produce an ultra-low roughness surface. AM printed parts have a typically granular and wavy surface, and the first step is to eliminate this granularity and reduce this waviness using a chemical process to bring the surface finish closer to that of a machined part. Once this is achieved, a chemical-mechanical process is employed to gradually and gently perfect the finish while maintaining the complex geometric features achievable using AM.
One of the biggest issues with AM production has always been surface finish. While dialing in parameter settings and improving the printability of metal powders is Elementum 3D’s forte, obtaining a near-perfect surface finish is REM’s. The marriage of these technologies has created an unparalleled surface finish in A6061-RAM2. “REM has worked with a number of AM-based aluminum alloys and the material that we have found to consistently have the best surface finishing potential is Elementum 3D’s A6061-RAM2 due to its high subsurface density.” Justin says.
To best illustrate the combined effect of our technologies, E3D and REM have partnered in producing and treating A6061-RAM2 LPBF manufactured piston heads and cylinders. The delicate and complex geometry of the parts is perfect for demonstrating how precisely material can be removed without altering the part itself. Below is an untreated piston head and cylinder as they are removed from the printer. We will share photos of the treated and finished parts in next month’s newsletter.
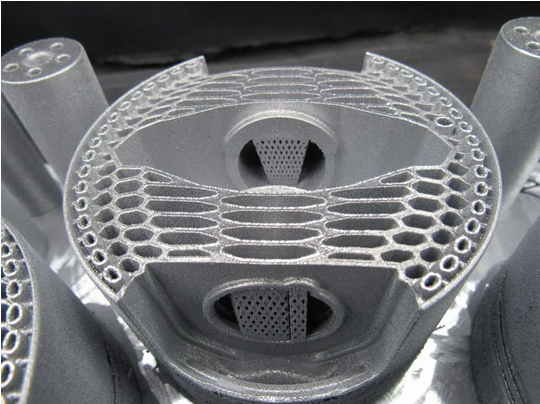

Upcoming Events
Formnext 2022 – November 15-18 | Frankfort, Germany
American Aerospace & Defense Summit – December 7-8 | Glendale, Arizona USA
SPEAKING EVENTS
MS&T22 (Materials Science & Technology) – October 9-12 | Pittsburgh, Pennsylvania USA
- Presentation Title: Permeable Additive Manufacturing (PermiAM) for Rocketry
- Presentation Title: Stainless Steel and Aluminum Alloy Development for Highly Consistent and Isotropic Properties in Laser Powder Bed Fusion
ASTM ICAM – October 31-November 4 | Orlando, Florida USA | Presentation Title: Use of Reactive Additive Manufacturing (RAM) techniques for new alloy and composite development
TMS 2023 Annual Meeting & Exhibition (The Minerals, Metals, and Materials Society) – March 19-23, 2023 | San Diego, California USA | Presentation Title: Using analytical solidification models to solve solidification cracking in laser powder bed fusion processed Ni-based alloys

- IMTS 2022 Preview3D Printing Doubles Presence at Manufacturing Technology Show
- API leverages standards to foster innovation and adoption of 3D printing
- Boeing and Northrop Grumman Commit to Additive Manufacturing Initiative
- Nikon Buys SLM: Consolidation Coming To 3D Printing?
- What are the challenges around using additive manufacturing for production?
- US Air Force Funds SLM Solutions via CTC to Build “World’s Largest” PBF Metal 3D Printer
- How is additive manufacturing favoring the industrialization of various sectors?

Army & Navy STTR Phase I projects kick-off
Elementum 3D recently began work on an Army STTR project that partners with Georgia Tech and Addiguru to improve the reliability of large-format cold spray additive manufacturing (AM). Cold Spray AM offers extremely high deposition rates with the ability to produce large-scale components. With more precise monitoring and control of the deposition process, denser, more dimensionally accurate parts can be achieved to reduce the post-processing time and costs.
With improved process feedback and control, this project intends to demonstrate cold spray additive manufacturing as a highly capable method for producing needed parts near the battlefield or at the point of use, reducing the logistical burden and improving readiness compared to having central storage and transportation of replacement components.
In a second project, Elementum 3D is working on a Navy STTR contract in collaboration with Ohio State University’s Center for Design and Manufacturing Excellence. This project is focused on development of a robust and reliable additive manufacturing and post-processing workflow for printing high-power, vacuum electron devices (VEDs) and radiofrequency (RF) components from a heat dissipating and corrosion resistant copper-nickel alloy. VEDs and RF waveguides and other components are often complex to produce, requiring manual bending and joining processes.
Successful additive manufacturing of these components will allow for faster, more economical production and innovations in printing complex assemblies and networks of components with improved performance.
Ursa Major partners with Elementum 3D to increase propulsion
Rocket propulsion manufacturer Ursa Major and Elementum 3D have more in common than having their headquarters in Colorado, they both strive to build the highest performing components using additive manufacturing (AM) technology. This unified desire was put to the test when Ursa Major challenged themselves to create a more sustainable copper combustion chamber to support the U.S. propulsion industry.
Ursa Major partnered with Elementum 3D to print a copper alloy combustion chamber that would be lighter, more reliable and with better engine performance. They relied on Elementum 3D’s expert knowledge of their proprietary copper materials and printing processes to effectively print a chamber that would allow for increased propulsion.
Working in tandem with Elementum 3D proved to be the right choice for this project. Our intimate understanding and proficiency in printing quality copper components made it possible for Ursa Major to 3D print their next-generation combustion chamber out of copper. Advancements in propulsion systems like this project are the key to a sustainable aerospace industry and it’s nice to know that Colorado companies remain at the forefront.
Cyber security initiative update
Elementum 3D continues to put the utmost importance on protecting the confidentiality, integrity, and availability of information and data. As part of this ongoing priority, Elementum 3D has proactively enrolled in a National Security Agency (NSA) program offered to the US Defense Industrial Base to perform vulnerability scanning to assess our networks and systems for vulnerabilities and facilitate security improvements where applicable. Elementum 3D values the confidentiality of data in our possession and strives to meet and exceed compliance requirements.