
RAM technology is solving the Navy’s need for a reliable AM-ready high temperature material
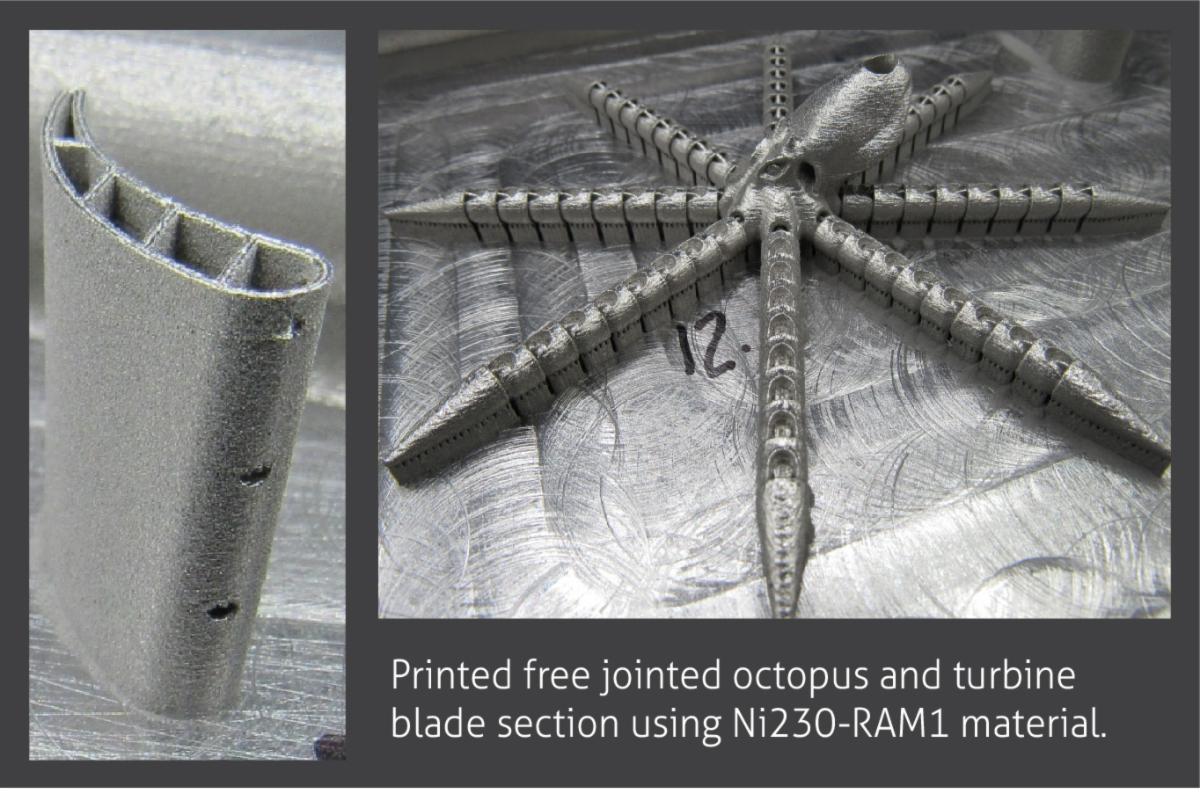
As of August 2023, Elementum 3D is halfway through a two-year Phase II SBIR project funded by the US Navy. The first year laid the groundwork for a viable solution to the SBIR objective: secure the ability to print reliable, high performance nickel-based spare parts and components in short lead times to repair and maintain critical equipment and readiness. The challenge is to develop a computational modeling framework for rapid alloy development and testing or maximizing alloy printability and performance.
In collaboration with Colorado School of Mines researchers, Elementum 3D recently developed a solidification model that facilitates to rapid development of its Reactive Additive Manufacturing (RAM) formulations for highly printable and superior nickel superalloys. The model includes the effect of RAM-formed inoculants to predict the extent of cracking during printing. The initial application of the model was to solve cracking issues in Alloy 230, and the resulting formulation (Ni230-RAM1) showed no cracking and 60% higher yield strength than wrought Alloy 230. Currently, primes can’t supply crack-free high-temperature nickel superalloys for AM because without RAM, they don’t exist. Elementum 3D’s RAM technology enables new application pathways for additive manufactured components where lower strength, traditional wrought material can’t be used.
Additional advantages of the RAM-based solidification model:
- Reduction of cost and lead time to produce replacement components and spares by 1.5-2x.
- Highly printable, crack-free, fully dense, and often stronger that wrought material.
- 6x elongation at break compared to unmodified printed Alloy 230.
- 7x longer creep life than unmodified printed Alloy 230 and comparable to wrought creep performance.
- More robust supply chain through distributed production.
- Expansion of range of printable nickel materials to inspire innovative applications.
- Increased component efficiency and performance at higher operating temperature
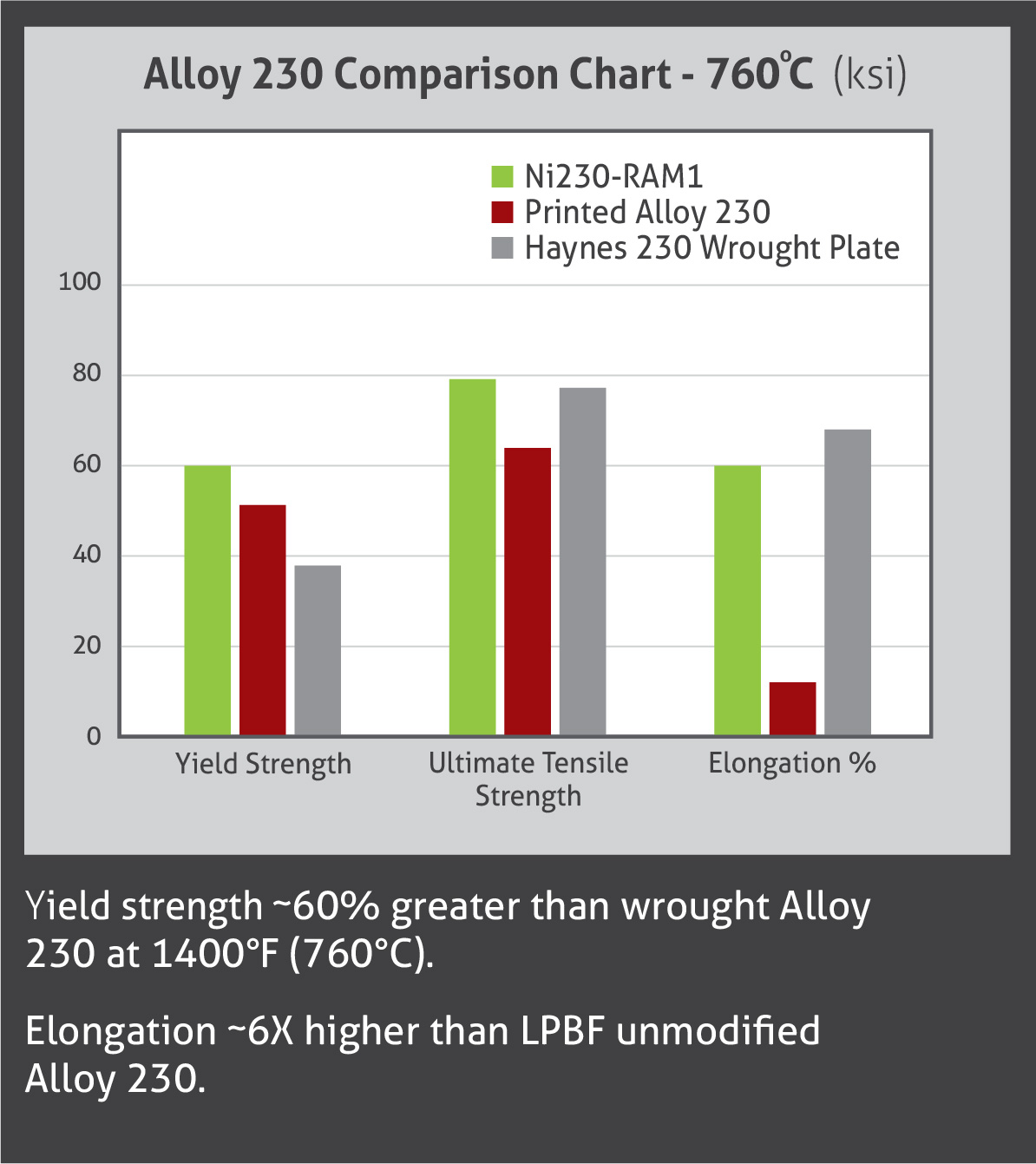
AM-ready high temperature materials, such as Ni230-RAM1 are targeted towards mission-critical applications in government, aerospace, space, and marine systems where performance, lead time, and resilience are at a premium. The defense sector urgently needs innovative AM feedstock materials to maintain legacy equipment, enable new and powerful propulsion, energy generation, weapons platforms, and structural systems and components.
The RAM process has expanded the library of high-performance AM materials. These products deliver fast and flexible AM capability to the supply chain while improving materials performance compared to traditional manufacturing. Other industries requiring exact materials property ranges for mission-critical projects with repeatability and access to large quantities of feedstock are proving out the success of the RAM approach, and Elementum 3D is currently supplying an automotive customer with over 20 tons of feedstock per year.
Recently, Elementum 3D joined the Navy’s SBIR Transition Program (STP) to connect with Navy stakeholders in urgent need of printable high-performance alloys. Ni230-RAM1 is already available for testing and producing real world components!

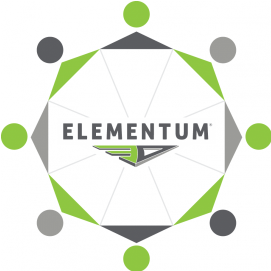
Employee Update
New Employees
Dave Scarano, Account Manager
Daniel Edwards, IT Support
Noah Wieber, AM Technician I (rehire)

- A Window of Opportunity to Accelerate Alloy Development for Additive Manufacturing
- America Makes announces two new project calls worth $11.75M to advance additive manufacturing technology
- Cargo Bikes Gets a Lightweight Lift with 3D Printing
- EXCLUSIVE: How the Navy’s chief engineer sees 3D printing rebuilding the fleet
- The Many Ways F1 Teams Have Put 3D Printing into Motorsports
- Dream Mergers and Acquisitions: Who Merges Next in 3D Printing?
- Additive Manufacturing powers mass production of medical components
- Special Focus Issue: Additive Manufacturing
- This Sector is Skyrocketing, and Businesses Using it to Reinvent Operations Will Soar
- Metal additive manufacturing results in Rocket Turbopump Design
- Totally tubular: New way of 3D-printing fuel cells could support renewable energy
- US Army Looks to Ramp up 3D Printed Auto Parts
- What’s taking shape with additive manufacturing and robotics?
- Additive Manufacturing in Aerospace: Advantages, Applications, and Materials