(ERIE, COLO., December XX) Elementum 3D, a leading developer and supplier of metal additive manufacturing (AM) advanced materials, print parameters, and services, is pleased to announce the official commercial release of GRX-810. This printable nickel cobalt chromium oxide dispersion strengthened (ODS) superalloy was first developed by Dr. Tim Smith and team at NASA Glenn Research Center and is now commercially available from Elementum 3D through a co-exclusive licensing agreement. Elementum 3D shipped the first commercially produced GRX-810 material to a customer on October 31st and has capacity in place for production of 1 ½ tons of GRX-810 per week. With this advancement, NASA’s goal to quickly accelerate the adoption of GRX-810 to benefit U.S. technologies is ahead of schedule.
“I’m proud of how the Elementum 3D team rallied to quickly bring NASA’s GRX-810 alloy to market. Development of a qualified manufacturing process to mass produce GRX-810 in six months is a testament to our ability to turn concepts into reality,” said Dr. Jacob Nuechterlein, Elementum 3D CEO and Founder.
This achievement is welcoming news for engineers eager to take advantage of the exceptional material properties offered by GRX-810 combined with the design complexity enabled by additive manufacturing. Potential breakthroughs enabled by this printable material include lighter and thinner engine parts, increased fuel efficiency, lower operating costs, increased durability, and higher operating temperature capability. Manufacturers in aerospace, space, and energy are particularly interested in this groundbreaking 3D printable high-temperature superalloy material.
At high temperatures GRX-810 offers 1,000-fold better creep resistance with a two-fold increase in strength and oxidation resistance compared to other available printable superalloys. The chart below provides typical performance data from NASA and Elementum 3D for powder bed fusion laser beam (PBF-LB) printed GRX-810.
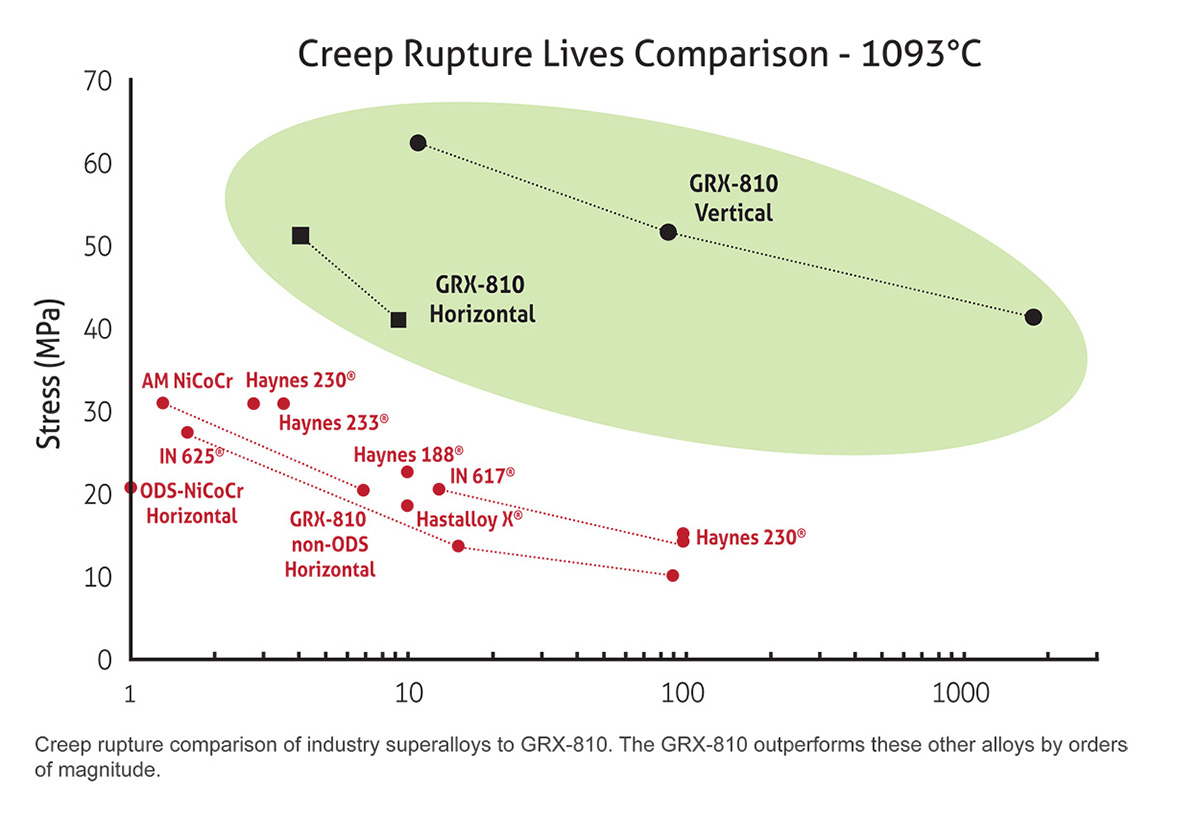
Creep rupture comparison of industry superalloys to GRX-810. The GRX-810 outperforms these other alloys by orders of magnitude.
Creep life is the duration a material can withstand continuous stress at high temperature without failure. Creep is a primary failure mechanism for parts at high temperatures subjected to loads from centrifugal forces, gravity, pressure, or other long duration stresses and so enhanced creep performance can directly lead to longer part life and higher operating temperature and load capability. For more information about Elementum 3D and its product offerings, please visit www.elementume3d.com or contact sales@elementum3d.com.