
High-performance metal 3D printing alloys take hold at Rapid+TCT
For Elementum 3D, this year’s Rapid+TCT event marked a transition from needing to educate the industry about our patented reactive additive manufacturing (RAM) technology and commercially available high-performance additive manufacturing (AM) materials to customers telling us about their active AM projects and production already taking advantage of our high-performance materials with amazing results.
Our materials experts were engaging in completely different conversations throughout the three-day event. AM users were revealing the projects and applications that have been greenlit to print with high-performance aluminum alloys. They also explained that the decision to move to higher performance alloys was based on analysis of how printable aluminum alloys have evolved from a single casting alloy (AlSi10Mg) to enhanced AM versions of high-strength wrought aluminum alloys like 6061, 2024, 7050, and 7075. Moreover, advanced dispersion strengthened alloys like A1000-RAM10 are gaining traction due to their high specific stiffness, reduced CTE, wear resistance, and excellent performance at elevated temperature.
Service bureau partners also chimed in with specific comments related to increased print orders with our materials beyond Elementum 3D’s involvement. This transition is directly related to our overarching plan to expand their line of printable materials to support the customer’s growing AM demands. “Greater adoption of printable high-strength aluminums and other advanced alloys is a complicated and slow process, but it’s all worth it when our team was fortunate to experience the shift to acceptance first-hand at Rapid,” said Steve Wagner, VP Sales at Elementum 3D.
The transition to advanced manufacturing processes offers a unique opportunity to choose the right material for the application and take advantage of high-performance materials coupled with improved part design. The interactions at Rapid provided an exciting opportunity to observe the embrace of new generation materials by designers, engineers, and decision makers to enhance performance, extend part life and reduce total cost. All industries can benefit from new technologies and innovative materials and we can all celebrate the mindset of leadership and innovations that are helping build a better future.
Elementum 3D builds upon existing cyber data protection procedures
In today’s world, cybersecurity is a key issue for virtually all organizations. Critical infrastructures, including advanced manufacturing, are regularly targeted by activists, nation-states, competitors, and criminals seeking profit.
Elementum 3D is on the leading edge of today’s digital manufacturing landscape and we take seriously our responsibility in managing the potential new risks and challenges the Fourth Industrial Revolution brings. We are vigilant about protecting data confidentiality, integrity, and availability and are compliant with the National Institute of Standards and Technology (NIST) Special Publication (SP) 800-171.
NIST SP 800-171 provides an outline of 110 controls for protecting Controlled Unclassified Information (CUI) in nonfederal systems and organizations. These controls align with cybersecurity best practices, and the provided recommendations can serve as a good foundation even for organizations not handling government CUI. The NIST SP 800-171 controls also serve as the core of Defense Federal Acquisition Regulation Supplement (DFARS) clause 252.204-7012 and the Department of Defense Cybersecurity Maturity Model Certification (CMMC) program. We are continuously evaluating and improving our cybersecurity policies, procedures, and controls and intend to become CMMC certified once DoD auditors are available for us.
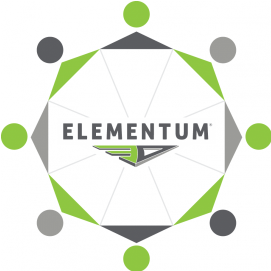
Elementum 3D Job Opening

- 3D printing industry hails Biden’s AM Forward initiative as “solid step forward” for the technology
- FACT SHEET: Biden Administration Celebrates Launch of AM Forward and Calls on Congress to Pass Bipartisan Innovation Act
- The 3D printing industry responds to Biden Administration’s AM Forward initiative
- DARPA Tasks Elementum 3D to 3D Print World’s Rarest Metal
- Larsen Motorsports and Florida Tech kickstart official affiliation with 3D printed dragster parts
- Shell 3D Prints Impellers for Its Dutch Refinery
- Will 3D printing become the new manufacturing standard in dentistry?
- Comment: How the demands of space are driving additive manufacturing development
- How AM is Disrupting the Aerospace Industry
- NASCAR to Implement 3D Printed Parts in Next Gen Racecars

Elementum 3D secures DARPA funding to develop printing process for rhenium metal
Elementum 3D has been awarded a Direct to Phase II SBIR contract from DARPA to develop a robust, economical additive manufacturing (AM) process to fabricate complex-shaped components from the refractory metal rhenium (Re).
As a refractory metal, rhenium can withstand high heat and has the 2nd highest melting point of all metal elements behind only tungsten. For this reason, rhenium is sought after as a component material capable of increasing the performance and extending the life of rocket and missile propulsion systems.
While rhenium has significant usage as an alloying constituent in nickel-based superalloys, its use as a base alloy is limited due to difficulty in traditional processing of this material. Forming rhenium into the complex shapes necessary for these applications is currently costly because of its high melting temperature, and it is an extremely difficult material to machine as it undergoes extensive work hardening. Additionally, some geometries are simply inaccessible with available machining and forming methods. A major initiative of the awarded SBIR is to research and develop an AM fabrication route to print components with geometrical features that cannot otherwise be produced by traditional manufacturing processes including powder metallurgy (PM) and electrical discharge machining (EDM).
As a recognized industry leader in developing new materials and processes for printing complex components using laser powder bed fusion (LBPF), Elementum 3D has a proven track record in developing high quality, repeatable print processes for other refractory metals including tantalum, tungsten, tungsten heavy alloy, and tungsten-rhenium alloy. This experience will allow Elementum 3D to work efficiently and rapidly in establishing a rhenium feedstock supply chain and print process suitable for critical applications.
Elementum 3D’s work on this DARPA project aims to help develop and expand the market for rhenium for AM processing so that the material can be used to benefit a wide range of advanced propulsion and hypersonics applications at the lowest possible cost. Should the base effort prove successful, an “option period” contract may be exercised at DARPA’s discretion to perform component-level fabrication and testing that will help encourage commercial adoption of rhenium for AM.
DFARS 252.235-7010 – Acknowledgment of Support and Disclaimer: This material is based upon work supported by DARPA under Contract No. 140D0422C0003. Any opinions, findings and conclusions or recommendations expressed in this material are those of the author(s) and do not necessarily reflect the views of DARPA.
Elementum 3D and EOS partner to support first collegiate rocket launch
A group of engineering students at the University of Texas at Austin (UT) is striving be the first collegiate team to launch a liquid bi-propellant rocket to an altitude of 100 kilometers, to the Kármán line—the internationally recognized boundary between Earth’s atmosphere and space. To achieve this feat, Elementum 3D and EOS have partnered with the Texas Rocket Engineering Lab (TREL) team to push the limits of science and rocketry with the inclusion of additive manufacturing printer technology and advanced materials.
TREL’s innovative combustion chamber design was printed on an EOS GmbH M 400-1, using Elementum 3D’s advanced copper alloy. This component integrates a special injector design that increases chamber pressure for greater efficiency, and it is fully reusable and able to support up to 60-second firing durations. The choice to use a 3D printing process also allowed the chamber to be printed as a single piece to help guarantee fewer points of failure, enabled special channel geometries to maximize regenerative cooling with a minimal pressure drop, and greatly simplified the manufacturing of unique design capabilities such as regen cooling the lower flange.
TREL views Elementum 3D and EOS as incredibly valuable assets in helping them accomplish their goal to reach the stars with potentially the most efficient 3D printed rocket engine ever produced by a collegiate team!
SPECIAL NOTE: TREL was originally founded to compete in the Base 11 competition. The mission of the competition was to encourage an increased representation of inclusion for women and minorities in STEM. Due to the extenuating circumstances surrounding COVID-19, this challenge—and the $1 million prize—has since been canceled…but that hasn’t stopped the TREL team from propelling forward!
RAM aluminum alloys add competitive advantage to motorsports applications
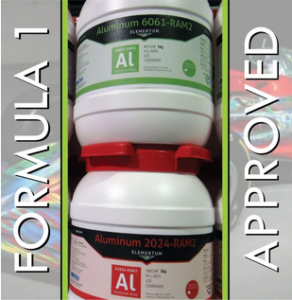
Join us at RAPID + TCT 2022 to discover what’s possible with metal AM powders
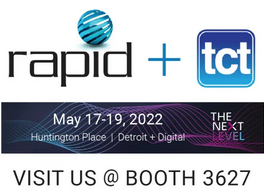
Additional reasons to experience RAPID + TCT 2022:
- TAP into North America’s most credible, comprehensive, and influential AM event.
- UNITE to share the latest trends in AM with 10,000+ AM professionals
- CONNECT with industry innovators as you explore the entire AM ecosystem
- DISCOVER solutions at 400+ exhibits
- EXPLORE new products – more are launched at RAPID than anywhere else
- LEARN from 200+ speakers, hosting 130+ technical presentations
- EXPERINCE insights from leading industry keynotes and thought leaders
- ATTEND the “AM Industry Celebration” – a can’t-miss networking event – OPEN TO ALL!
- DISCUSS Emerging trends with 60+ leaders
- INSPIRE others by sharing your story