
Air Force RSO expands A6061-RAM2 testing Agreement
The United States Air Force Rapid Sustainment Office (RSO) recently expanded their material characterization agreement with Elementum 3D (E3D) focused on specification, dataset generation, and application testing of A6061-RAM2 for laser powder bed fusion additive manufacturing. The newly exercised Option includes as-built fatigue, as-built and machined fracture toughness and fatigue crack growth testing, stress corrosion cracking testing, wear testing, and additional tensile testing. This testing will provide a more thorough understanding of A6061-RAM2 T6 material properties for specific applications and provide a robust dataset for part design and qualification.
As part of the project, Elementum 3D is developing a full dataset based on MMPDS S-basis guidelines as well as performing additional testing to consider the impact of wall thickness, as-built surfaces, and HIP on material properties and applications. The combination of material property characterization and application studies, including non-destructive testing evaluation and a prototype part study, will provide the RSO with information they need to start qualifying parts out of A6061-RAM2 on EOS M290 printers used for this effort.
The Elementum 3D team is excited to leverage their knowledge and expertise in materials development, specifications, and printer qualification towards the success of this project. Their active involvement in AMS AM Metals and MMPDS committees will be leveraged with industry experience in specification, dataset development, and qualification for AM materials.
As AM material experts, E3D is excited to work with the RSO to produce a robust material dataset, material and process specification, and application testing to enable use of this aerospace grade aluminum and additive manufacturing to support life cycle management and sustainment of the US Air Force.

Teammates bond at “Mudder”
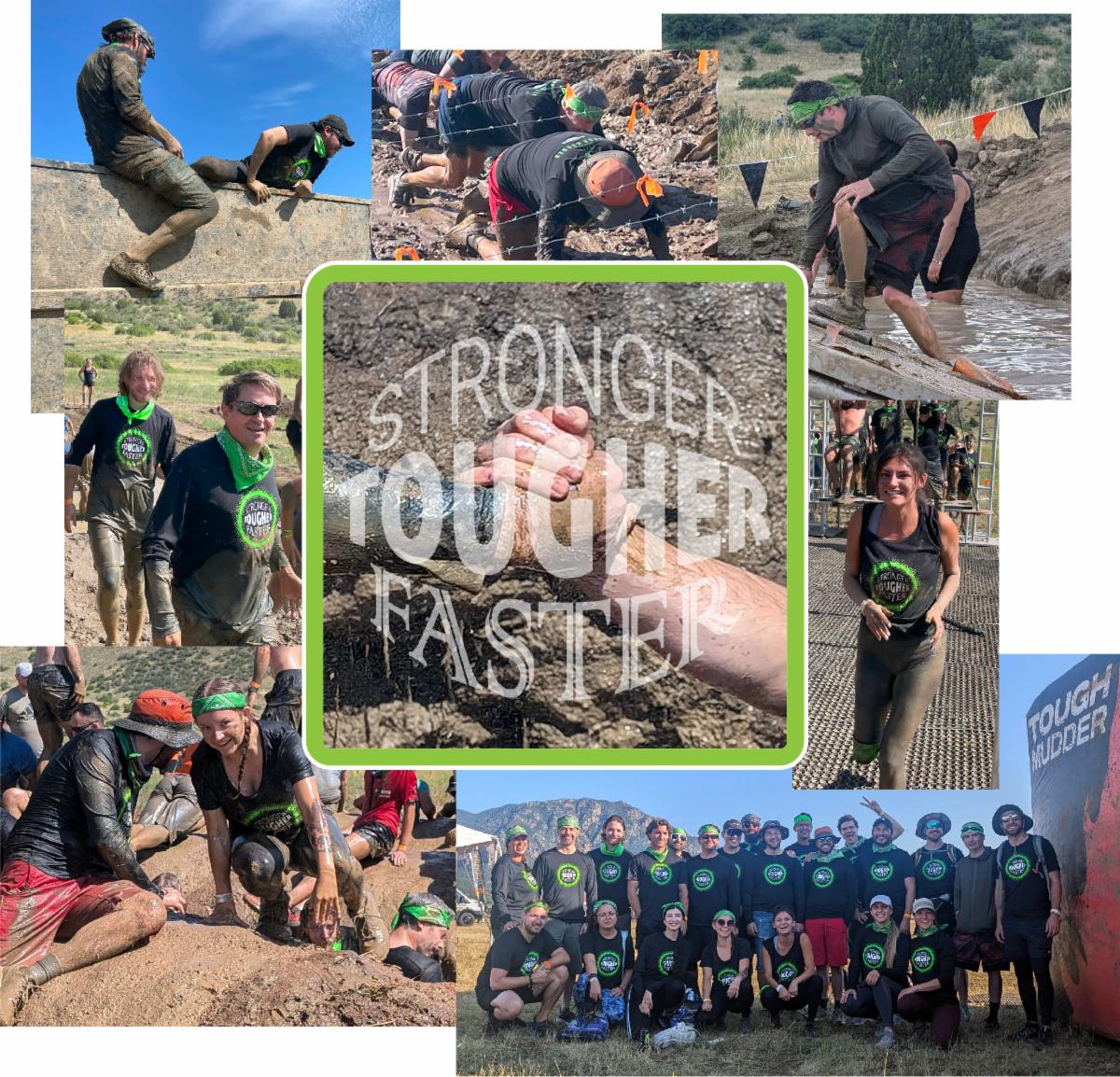
On July 20, Elementum 3D entered 15 employees along with 7 others outside the company in the “Tough Mudder” event held at Fort Carson, Colorado. All 22 competitors finished with their heads high and some bruises, scraps, and cramps.
This event went beyond running, jumping, climbing, swinging, and balancing, the “Elementum 3D Stronger, Tougher, Faster” team had to establish trust, communicate efficiently, and — most of all — lend a helping hand to conquer the 10+ mile course that included over 20 grueling and muddy obstacles.
Getting muddy together proved to be a fun way to build connections with teammates from different departments, improve company morale, and inspire some friendly competition.

- Agile Space Industries on the use of Additive Manufacturing in in-space propulsion systems
- Not a Metal 3D Printer: Arizona Startup Rosotics Launches the Halo ‘Supercreator’
- How SWISSto12 uses game-changing additive manufacturing in the SATCOM and RF sectors
- Paul Gradl, NASA: New Rocket Technology Enabled by Additive Manufacturing
- Westinghouse successfully uses additive manufacturing component
- “3D Printing: Shaping the Future with Precision and Innovation”
- Back to the Grind: It’s Time for the Additive Manufacturing Industry to “Collaborate” and “Do the Hard Work”
- 3D Printing Takes On New Automotive Dimensions
- McLaren Automotive to use Divergent’s Adaptive Production System
- Collins Aerospace on doubling down on metal additive manufacturing
- How robotics and automation can benefit from 3D printing, explains
- Rocket engine startup Ursa Major adds 3D printing lab in Ohio
- Governor of Michigan & Secretary of the Navy Announce Michigan Maritime Manufacturing Initiative