
A7050-RAM2 receives Aluminum Association registration
Elementum 3D, a leading developer and supplier of metal additive manufacturing (AM) advanced materials, print parameters, and services proudly announces the registration of its second powder feedstock material with the Aluminum Association (AA). In October, 2023, A6061-RAM2 was registered as 6A61.50, and now A7050-RAM2 has the designation of 7A50.50 with the AA. This endorsement further certifies the quality and printability of high strength AM aluminum alloys.
The Aluminum Association is a champion of global aluminum standards and sustainability. Beyond advocating for aluminum production, suppliers to the industry, recycling, as well as value-added products, the association is actively involved in sustainability research, business intelligence, regulatory and legislative policymakers, and the general public.
Elementum 3D’s A7050-RAM2 is an aerospace and specialty AM aluminum alloy that features a combination of high toughness, high strength, and good resistance to stress corrosion cracking. Like A1000-RAM10, A2024-RAM2, A5083-RAM2, and A6061-RAM2 aluminums, A7050-RAM2 utilizes Elementum 3D’s patented RAM technology, whereby feedstock powder and RAM additions are locally activated by the laser energy during the build process to produce product phases that act as nucleants for the aluminum alloy during solidification. These nucleants produce an equiaxed grain structure to solve the hot tearing and columnar grain problem.
For decades, AM enthusiasts have desired a wider selection of reliable, high-performance aluminum-based feedstocks for AM. We are honored to lead the advancement of metal AM alloy materials with the backing of the Aluminum Association. A7050-RAM2 has been available commercially since 2019 and can be purchased on the Elementum 3D website or by emailing our sales department.
NASA selects Elementum 3D as co-exclusive licensee of GRX-810 superalloy
Elementum 3D and NASA join forces again! This time we have been selected as one of four co-exclusive licensees of their latest breakthrough high-temperature additive manufacturing alloy — GRX-810.
The breakthrough 3D printable high-temperature metal superalloy powder will be offered to original equipment manufacturers of airplanes and rockets as well as the entire supply chain.
NASA’s goal of the licensing agreement is to quickly accelerate the adoption of GRX-810 to benefit U.S. technologies, industry, and space exploration. Engineers are eager to print with a material capable of creating lighter and thinner engine parts, reducing fuel burn, lowering operating costs, increasing durability, and lowering the tolerance for failure for critical applications.
GRX-810 is an oxide dispersion strengthened (ODS) alloy that can endure higher temperatures and stress. Its strength is derived from the dispersion of tiny particles containing oxygen atoms. The breakthrough superalloy was specifically developed for the extreme temperatures and harsh conditions of aerospace applications, including liquid rocket engine injectors, combustors, turbines, and hot-section components, capable of enduring temperatures up to 1,100 °C. Compared to other alloys, GRX-810 can endure higher temperatures and stress up to 2,500 times longer. It’s also 3.5 times better at flexing before breaking and twice as resistant to oxidation damage.
Over the past nine years, Elementum 3D has gained extensive knowledge and experience in developing, commercializing, and distributing “impossible-to-print” dispersion-strengthened materials similar to GRX-810. As the first to release a strengthened aluminum alloy, Elementum 3D is leader in the materials development field.
“We are excited to be working with Tim Smith and NASA to bring this exceptional new alloy to the commercial market,” said Jeremy Iten, Elementum 3D Chief Technology Officer.

Materials Consortium’s “Unlocking Key Materials in Metal 3D Printing” live event
We invite you to be our guest on June 24th from 6:30-9PM at the Mimo Technik Facility — 24426 S. Main St., Building 704, Carson, CA 90745 (18.1 mi from the RAPID+TCT 2024 event)
Don’t miss out on this special opportunity to be the first to learn about recent metal AM material
achievements and parameters development. Highlights of the event will include materials updates from Dyndrite, Constellium, Sandvik, and Elementum 3D.
Contact our sales department to be personally invited to an event that will unveil
how metal 3D printing materials can elevate component performance and lower
qualification cost and production cost.
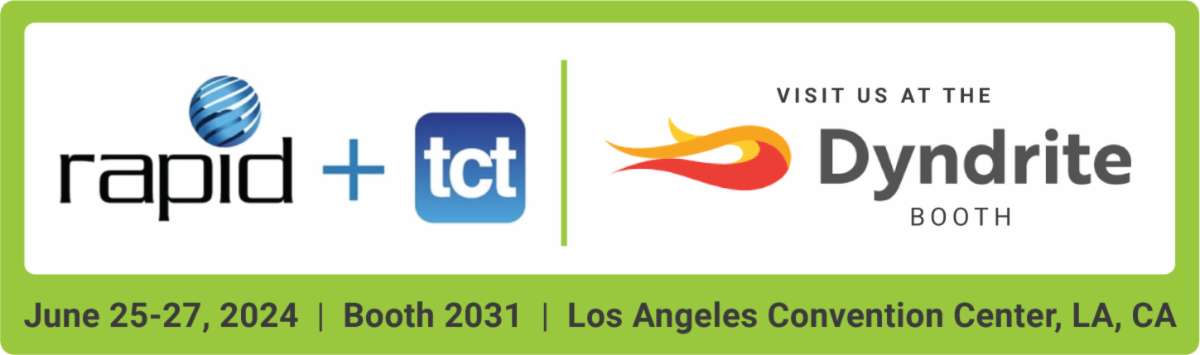

- The 10 Most Popular Metals in Metal 3D Printing
- 3D Printing Aluminum – The Ultimate Guide
- NASA Licenses 3D-Printable Superalloy to Benefit US Economy
- Laser Wars: Eplus3D Unveils Metal 3D Printer with up to 64 Lasers
- Chairman King Touts Defense Benefits of 3D Printing
- Apple said to test using 3D printers to make devices
- Ariane 6 launches Replicator for 3D printing in open space
- SWISS to12 develops new 3D printed antenna chains for Northrop Grumman
- GE Additive rebrands as Colibrium Additive
- Dyndrite awarded $1.3M from America Makes to improve LPBF OQ
- Driving a billion-dollar AM business in automotive
- Cobra Releases First Commercially Available 3D Printed Golf Irons
- Chuck Jaws Achieve 77% Weight Reduction Through 3D Printing
- Breaking Boundaries in Powder-Based Additive Manufacturing Technology Earns CAREER Grant
- Automated Quality Control for 3D Printed Metal Parts
- Additive Manufacturing Could Turn the Tides for Marine Energy Technologies—Here Is How
- 3D Printing’s Impact on the Supply Chain
- 3D Printing, The Bright Spot In U.S.-Based Manufacturing
- The use of aluminum in Additive Manufacturing: challenges and opportunities