PSP-AC’s propulsion team posing with the print of their TCA component.
Additive manufacturing (AM) is transforming the impossible into possible. It’s also transforming how the next generation of innovators will design and manufacture the products of tomorrow. The rapidly expanding successes in 3D printing space-related applications (i.e. NASA’s RAMFIRE program) have inspired a team of fifty enthusiastic undergraduate students on Purdue University’s Active Controls team to optimize the benefits of AM to advance vertical take-off and vertical-landing (VTVL) technology.
The Purdue Space Program-Active Controls (PSP-AC) team is under an umbrella student organization on Purdue University’s campus that aims to empower students to innovate in space exploration. Their current project satisfies the milestones of the Collegiate Propulsive Lander Challenge (CPLC) which has challenged student teams to create self-landing rockets. This challenge gave rise to PSP-AC’s TADPOLE propulsion system.
“This team operates under a greater vision to prepare the current and future classes of engineers to be more attuned to the current technological trends in space exploration,” said Pavit Hooda, PSP-AC project manager and co-founder.
The TADPOLE propulsion system is part of PSP-AC’s journey of creating a bipropellant hopper vehicle. Such a vehicle requires a propulsion system with long burn times, a regenerative cooling circuit, and thrust vector control capabilities. To produce a thrust chamber assembly (TCA) that can achieve these extreme specifications with complex geometries and precise tolerances, PSP-AC chose Elementum 3D to print the aluminum combustion chamber, cooling circuit, and nozzle in a single component using laser powder bed fusion.
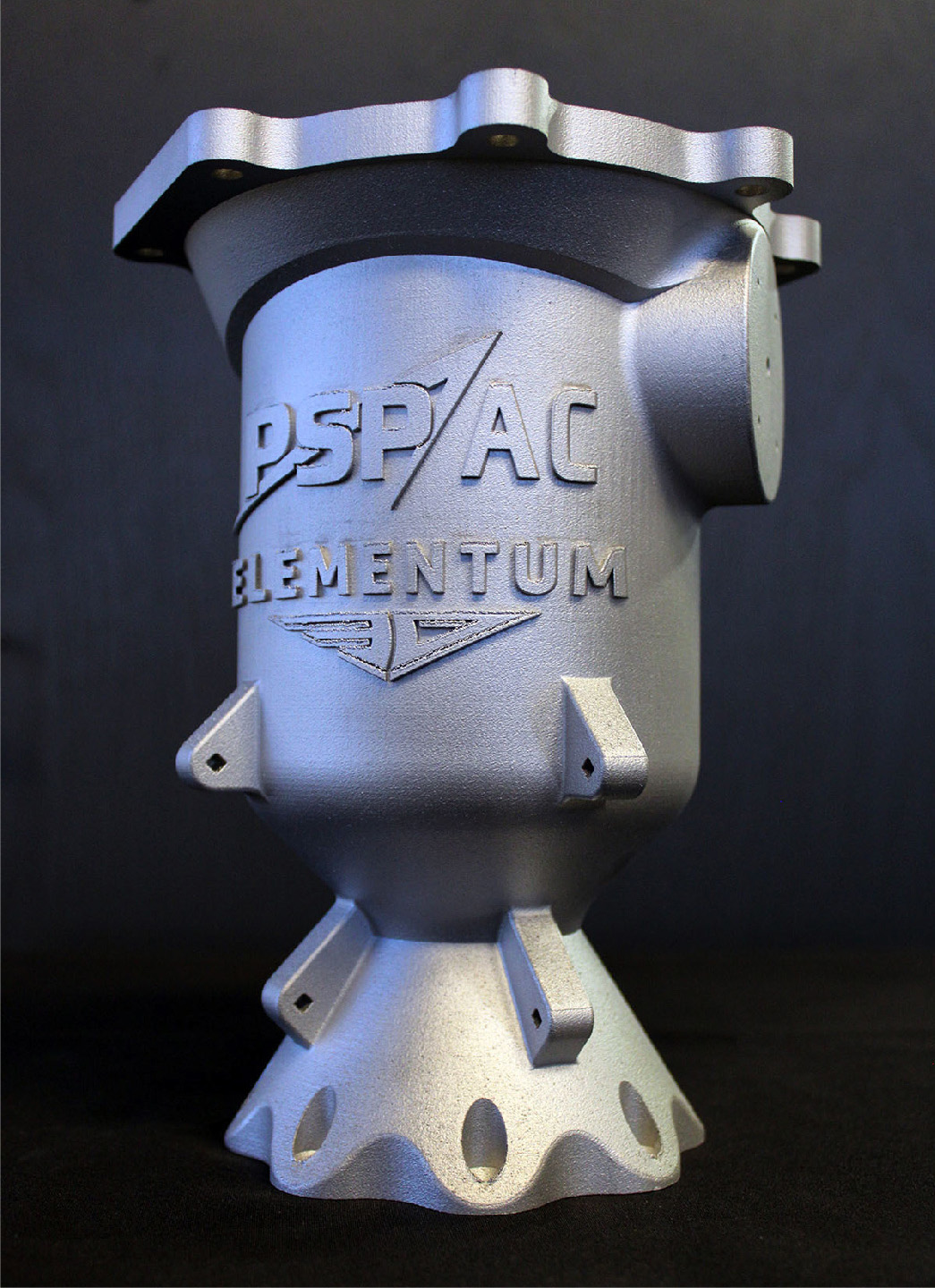
“We are honored to offer our team’s AM knowledge, expertise, and technology to inspire all the students involved in the Purdue Space Program to push the limits of conventional thinking and print the first ever A6061-RAM2 thrust chamber assembly,” said Dr. Jacob Nuechterlein, Elementum 3D founder and president.
At a chamber pressure of 250 psi and a thrust class of 550 lbf, PSP-AC determined that Elementum 3D’s advanced RAM technology was necessary for making this project a reality. The aluminum alloy A6061-RAM2 material provides the proper yielding characteristics required for the operating conditions of TADPOLE and offers an extended lifespan to the TCA enabling the team to include more tests in their test campaign, ultimately allowing them to learn more from this experience of designing and testing a propulsion system.
PSP-AC selected aluminum to print the thrust chamber assembly because of its great thermal properties, light weight, and low cost. The team was enthusiastic to discover Elementum 3D’s aluminum alloy does not have the drawbacks that we found with other AM aluminum powders, such as rough surface finish. The thrust chambers printed with A6061-RAM2’s had a very smooth surface finish, which is good for heat transfer and better thermal and mechanical properties than the competing alloys.
Another challenge of 3D printing a TCA is the post-processing and depowdering of the internal channels. The PSP-AC team worked very closely with Elementum 3D engineers to develop viable solutions and dimensions to allow for adequate powder removal. A big “a-ha” moment was realized when the team found it generally easier to depower than the industry standard GR-COP alloys, which is a big advantage. Additionally, the PSP-AC team enjoyed working closely with Elementum 3D’s engineers to get detailed material property information on the alloy, which was something they struggled to get from other vendors. This allowed them to understand and model the performance and functionality of the TCA and ultimately compare to experimental data generated during engine testing.
“The whole process is a great engineering challenge and learning experience that was made possible by Elementum 3D’s support. PSP-AC will use these simulations and experimental results to design their next engine,” said Andrew Radulovich, PSP-AC chief engineer.
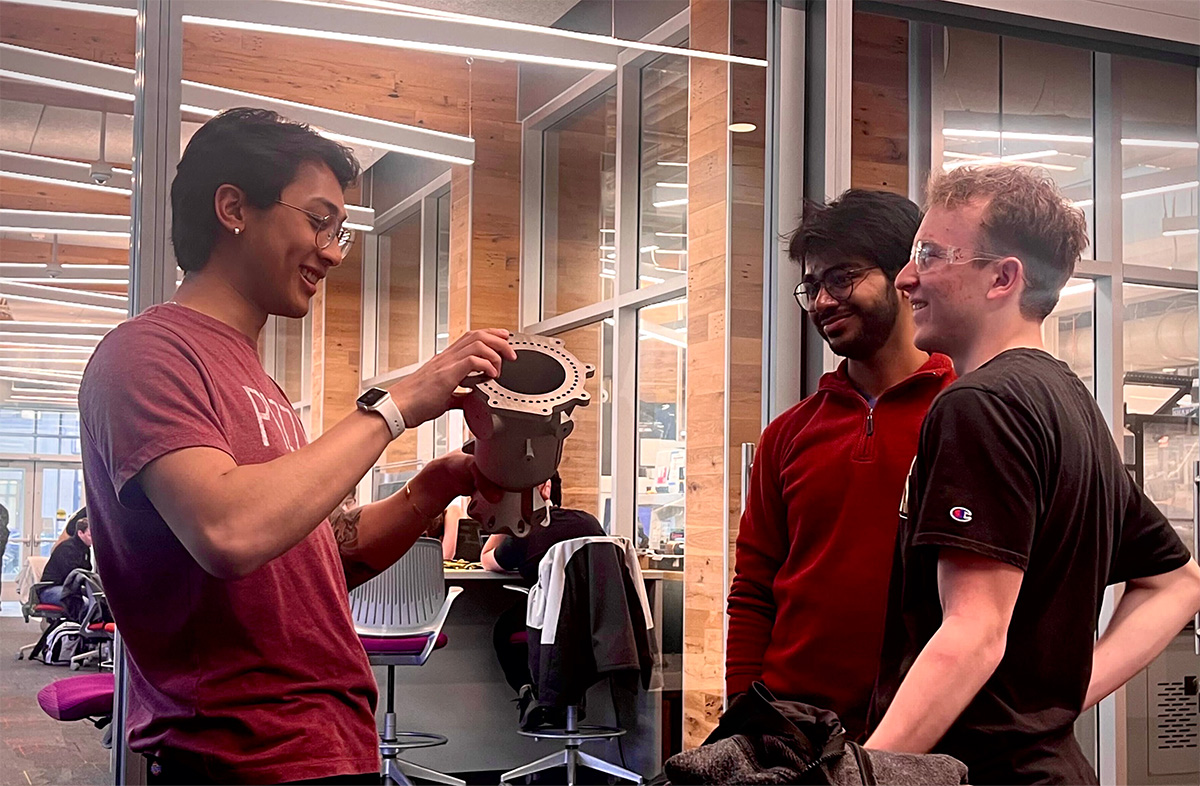
There are many organizations that are invested in the success of the PSP-AC team. We are delighted to be one of them. Aiding them in their journey to print an aluminum thrust chamber goes well beyond propelling space technology to greater heights; it ultimately builds confidence in the reliability and repeatability of AM.