
Elementum 3D Celebrates 10 Years of AM Materials Innovation
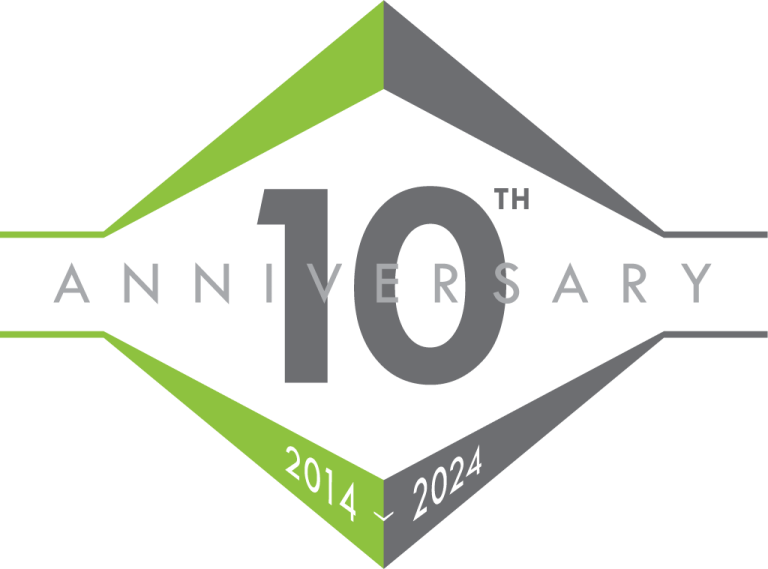
This October, Elementum 3D proudly celebrates 10 years in business and the ongoing commitment to push the limits of what is possible and expand the adoption of additive manufacturing (AM). Over the past decade, the company has grown from a concept developed in a small corner of a warehouse to a globally recognized leader in the development and supply of new and enhanced high-performance metal alloy powders.
Reaching this milestone is a testament to more than one or two people, it’s because of the initial and current investors, employees, and supporters that believe in the company’s ability to release groundbreaking materials into the AM community. They defined what Elementum 3D is as a company and what sort of difference it could make in the 3D printing industry. The success picture would not be complete without thanking our industry partners and all the third-party companies for their support and loyalty.
“I never would have predicted where Elementum 3D would take me. I’ve traveled all over the world, gone to factories, and worked with customers I would have never thought possible. It’s been incredible. I appreciate all those who have supported and even cheered on Elementum 3D from the sidelines over the past 10 years. I can’t wait to see what’s next,” said Dr. Jacob Nuechterlein, president and founder of Elementum 3D.
The original vision for Elementum 3D was to fill the huge metal materials gap in the AM market — the printability of metal alloy materials without compromising on material properties. The additive manufacturing industry was different in 2014, printable materials were extremely limited compared to CNC machine shop materials. The industry had to settle for what was out there. Elementum 3D thought differently, which has significantly impacted the adoption of AM as a viable manufacturing option.
Elementum 3D been scaling at an exciting pace every year and has established company fundamentals to effectively address the challenge of future growth. The next stage in the company’s journey is transitioning from supporting R&D programs and projects to full-scale production and commercialization. Leadership and staff are preparing to match the large materials orders associated with the next phase of AM to fend off shortages in raw materials, which can often choke an industry.
“We’re seeing the AM industry shift from hypothetical to the real phase of commercialization, this transition to serial production capability and capacity will be the most exciting thing I’ve seen or been a part of since Elementum 3D was founded in 2014.” Jacob goes on to say, “everything leading up to now has been practice, preparing to be ready for the real show.”
For more information about Elementum 3D and its 10 years of service, visit www.elementum3d.com
Sign up for the Bridging the Gap webinar on October 30th, at 11am EDT to learn how Elementum 3D and Continuum are transitioning the supply chain process from a challenge to an opportunity.
Current hurdles in sourcing and maintaining a consistent supply of high-quality AM powders and how to address these issues is the focus of the 1-hour Bridging the Gap webinar. Materials experts will share the most recent advancements in optimizing AM supply chain to dramatically reduce supply chain disruptions and the newest technologies capable of producing the highest quality powders on the market.
Webinar takeaways:
- Recycling scrap metal contributes to a more sustainable and efficient AM process, reducing waste and optimizing material usage.
- Importance of sourcing and maintaining a consistent supply of high-quality AM powders.
- Improving key material properties like flowability, density, and particle size distribution to enhance AM performance.
- Importance of traceability and integration of real-time quality control for better transparency and certification.
- Expanding the materials library for LPBF to improve design possibilities and economic concerns for AM parts.
- New alloy design and material production methods to expand AM application spaces and increases sustainable advantages for AM production.
- Robust datasets for newer AM specific alloys to help support part designers and producers with reference properties.
Trade shows
Formnext: Booth 11.1-D57 | November 19-22, Frankfurt, Germany

- Challenges and opportunities in additive manufacturing
- AM Research notes year-over-year industry growth of 8.4% in second quarter data report
- 3D printing reduces brake disc emissions by 27% to meet the EU’s new vehicle requirements
- Lockheed Martin 3D printing new Mako hypersonic missile
- Revolutionizing the Skies: The Role of 3D Printing in Aerospace Innovation
- Ursa Major Leading New DOD Project to 3D Print Solid Rocket Motors in the US
- ATI additive manufacturing strategy targets order of magnitude growth in number of flying 3D printed parts in UK
- Behind the scenes of the first metal part to be 3D-printed aboard the ISS
- 3D printing-enabled race car victorious at 2024 Formula Student Austria
- ADDMAN’s acquisition of KAM said to create largest metal AM service provider in North America
- 3D Printed Engines Propel Next Industrial Revolution
- Northrop Grumman revolutionizes aerospace with digital engineering
- 3D Systems receives FDA approval for new 3D printed surgical guides
- SpaceX signs 3D printing deal with Velo3D