Understanding Metal Matrix Composites
What is a Metal Matrix Composite (MMC)?
Throughout history, materials have defined our technology and fueled creative thinking to solve our problems and advance our capabilities. Today, engineering materials are often classified into categories, with the four major groups comprising metals, polymers, ceramics, and composites. Metal based composite materials, known as metal matrix composites (MMCs), are one of the major innovations in materials science and engineering since the late 19th century.
Composites are materials composed of at least two distinct constituent phases. Metal matrix composites have a continuous metal matrix phase and one or more additional phases such as ceramic reinforcements. The combination of different materials can produce a unique and advantageous set of properties with the freedom to tailor the properties to specific application requirements by varying the fraction of reinforcement material, the size and shaped of the reinforcement, and the production method. Desirable properties associated with MMCs include increased specific strength, stiffness, wear resistance, high temperature performance, corrosion resistance, thermal and mechanical fatigue resistance, and creep resistance. metal matrix composites provide a great degree of versatility. For example, an aluminum MMC is often used for applications requiring light weight, high specific mechanical properties while nickel MMCs provide the ability the retain excellent mechanical strength, resist oxidation, and reduce thermal creep at extreme temperatures.
Metal matrix composites are becoming important high-performance materials for aerospace, automotive, and defense because of their enhanced physical properties including excellent specific performance. MMCs are applied in satellite structures, helicopters, turbopumps, compressor blades, jet-engines, high-temperature components, brake rotors, pistons, cylinder liners, structural automotive components, machinery components, defense applications, recreational equipment such as golf clubs, bicycles, and the list goes on. For many of these applications, the significant advantages of MMCs can directly result in performance benefits such as energy savings and increased component life.
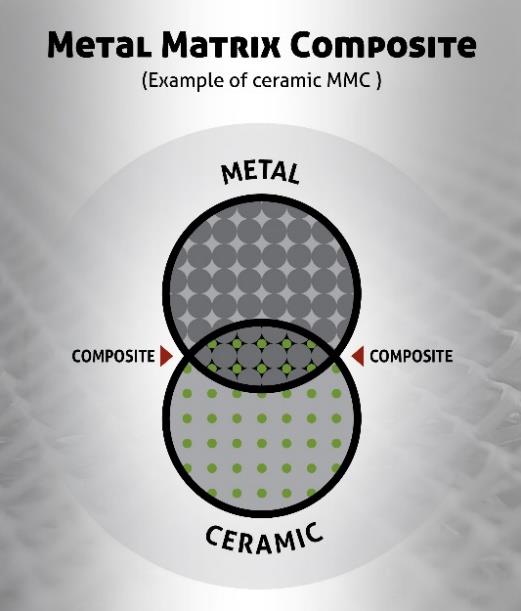
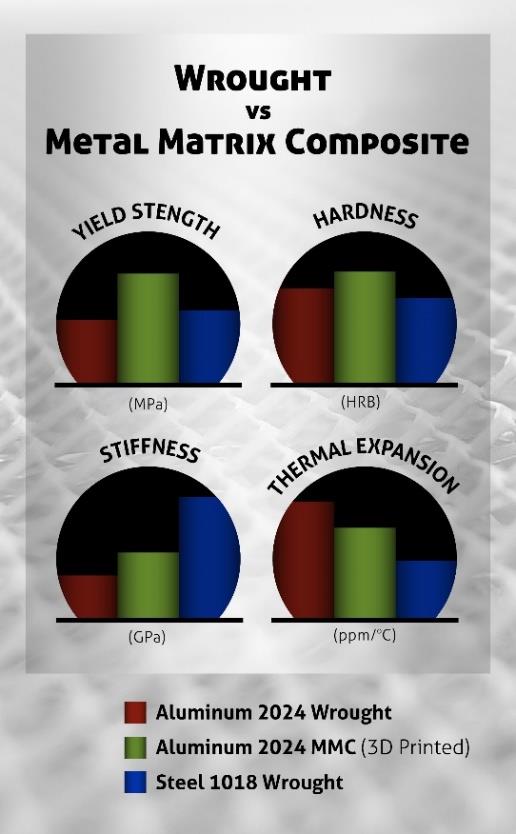
Why isn’t everyone using MMCs?
So, how come these superior materials haven’t stolen the hearts of manufacturers around the world? It’s because the process to produce MMCs must overcome specific challenges to realize their full potential.
Key challenges of MMCs compared to metal alloys are:
- Higher cost of material production
- More difficult to cast, forge, form, etc.
- Difficult/expensive to machine
- Limited service experience/heritage
- Stir-cast MMC components often have particle agglomerates that may result in premature failure.
Component cost is a key concern in commercial markets especially at high-volumes. Compared to non-composite alloys, traditionally manufactured MMC components are usually more expensive due to more costly material production and component fabrication techniques. Additional costs are incurred from the extensive research needed for new material development and application qualification testing.
Conventional production of metal matrix composites has been accomplished by liquid state (stir-casting) and sold state (powder metallurgy) processes. Of the two approaches, liquid state processing is the most economical approach for high volume material production. The main limitations of stir casting include difficulties with particle agglomeration in the metal melt, casting challenges stemming from high melt viscosity, and more difficulty with secondary processing than traditional alloys. Powder metallurgy processes face difficulty sintering MMCs to high relative density and high process costs including molds, dies, and post processing. To summarize, conventional MMC production processes struggle with defects including particle agglomeration and porosity and face high processing costs to produce net-shape components.
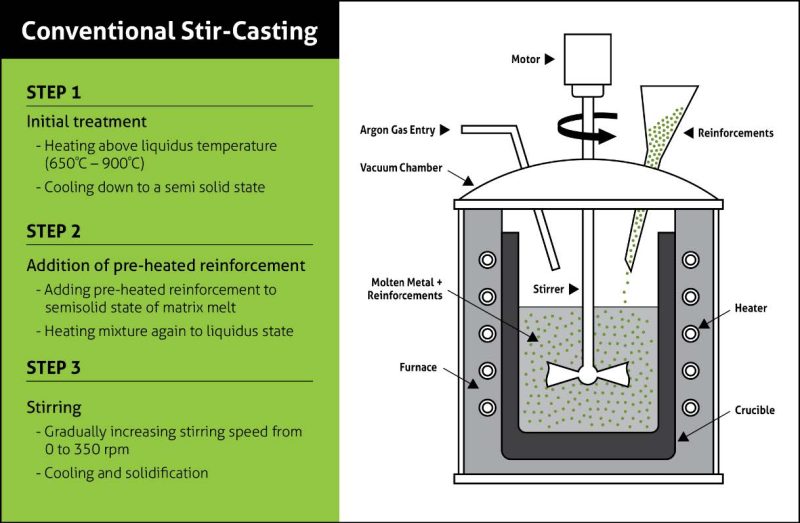
Based on these conventional process limitations, how liberating would it be to produce MMCs with the transformative advantages of additive manufacturing (AM)? Additive manufacturing offers the ability to produce net-shape components directly from feedstock material, control the microstructure at the micron level to minimize defects, and provides the freedom to design-in high part complexity. What if the advantages of additive manufacturing could be used to produce complex components from high-performance MMC materials?
Why use Additive Manufactured MMCs?
Additive manufacturing is one of the fastest growing design and production processes in the world and has only begun to scratch the surface of its enormous potential. It offers end-users the ability to efficiently develop prototypes and production parts without the need to invest in costly tooling and molds, produce near net shape parts with complex features and consolidate parts to increase strength, reduce weight, and simplify design and assembly. Even with these compelling benefits, AM is still an emerging industry and has many obstacles to overcome to fully mature as a widely used manufacturing option. Limited AM material options are one critical obstacle to widespread AM adoption.
High-performance metal matrix composites for AM can provide significant and disruptive benefits to industry, military, and environment. Imagine the transformative effect MMCs can provide through reduced weight, improved stiffness, higher specific strength, increased use temperature, and improved life. MMCs materials take advantage of the benefits of additive manufacturing by enabling fabrication of complex components, reducing fabrication and transportation energy requirements, reducing waste, and eliminating dies, molding, and tooling. By reducing the number of individual MMC components and therefore the number of connecting structures required for a part assembly, the weight of the assembly can be reduced. Component weight reduction will result in reduced fuel consumption and emissions as well as increased performance and payloads.
Additive manufactured MMCs offers end-users several key benefits compared to traditionally produced MMCs. The small melt pool produced in laser powder bed fusion (L-PBF) is beneficial for producing a repeatable and uniform microstructure. Production costs can be reduced because the net shape production minimizes materials waste and reduces finishing requirements. Design improvements enabled by additive manufacturing have been shown to result in significant energy and environmental savings during the service life of the component. Additional energy savings result from eliminating the need to melt excess material, further reducing waste and emissions. Users can also realizes saving in personnel, reductions in dedicated floor space for manufacturing, as well as the ability to carry less inventory.
Rising commercial demand for high-performance materials from automotive, aerospace and marine industries is expected to remain a key driving factor for the MMC market. For example, the need for automotive curb weight reduction to increase fuel-efficiency and reduce pollution is expected to influence MMC usage in automotive production. The introduction of additive MMCs could significantly boost MMC demand by alleviating historical challenges in manufacturing complexity, cost, and time.
Why haven’t MMCs been available in additive manufacturing?
Additive manufacturing is celebrated for its process versatility and freedom to fabricate complex components and consolidate designs that would traditionally require welding and joining of many parts, but customers have precious few freedoms in metal-based material choices. Today, traditional manufacturing offers over 5,000 metal-based materials choices, while commercial AM metal-based materials are primarily limited to select alloys of maraging steel, stainless steel, cobalt-chrome, Inconel, titanium, and aluminum. Metal matrix composites were not on the AM list of available materials because existing AM processes could not adequately produce near net shape components with near full relative density with good mechanical performance. Efforts to print many commonly used traditional alloys have also been unsuccessful due to the same difficulties.
Is it possible to 3D print MMCs?
Elementum 3D has demonstrated an innovative process termed reactive additive manufacturing (RAM) to
successfully fabricate complex metal matrix composites parts. The RAM process can overcome the obstacles
typically faced during development of AM materials. Elementum 3D’s RAM process utilizes in-situ chemical
reactions to produce advanced materials that outperform existing printable materials. Elementum 3D’s RAM
process can use existing AM equipment by utilizing a RAM feedstock material and custom processing parameters.
Elementum 3D has shown that the RAM process enables ‘unprintable’ aluminum alloys including 2024, 6061, and
7075 to become readily printable as metal matrix composites. Elementum 3D’s 2024 aluminum matrix MMC
exhibits 2.3x the yield strength, 1.7x the ultimate tensile strength, 1.4x the elastic modulus, and 3.8x the wear
resistance of AlSi10Mg, the only widely used aluminum alloy for L-PBF AM. Figure 1 provides an example of the
capabilities and complexities enabled by RAM materials.
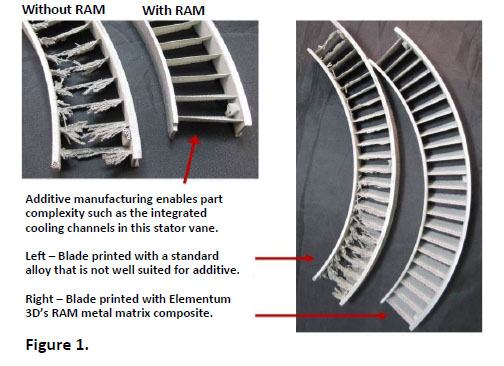
Early research results have demonstrated success with fabrication of fully dense nickel superalloy MMC parts with
excellent microstructures free of microcracking. Results also indicate the process to be applicable to fabrication of
components from composites with matrices of nickel, Inconel 625, and Inconel 718. Significantly, it was found that
the RAM process produced MMCs with improved microstructures compared to the commercial base alloys. An
example of a RAM produced Inconel 625 MMC micrograph exhibiting significantly reduced microporosity is shown
next to a micrograph of an industry standard Inconel 625 in Figure 1.
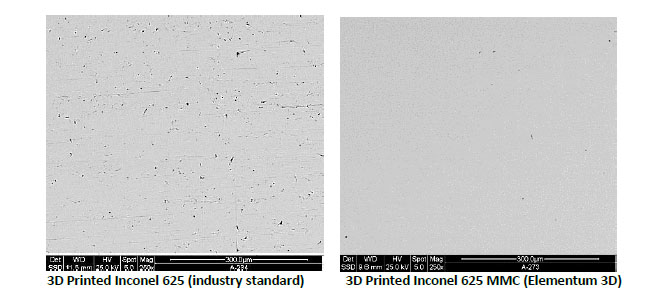
In addition to reduced microporosity, the formation of the reinforcing ceramic particulates resulted in MMC parts that were significantly harder than the base alloys which is indicative that the MMC material will have improved strength compared to the base superalloys. In addition, the high thermodynamic stability and high melting temperature of the reinforcing ceramic lends itself to improved high temperature performance compared to the base alloys.
The marriage is revived
Materials are the life blood of additive manufacturing and Elementum 3D’s RAM technology is energizing the AM industry. The introduction of MMCs optimizes the already mind-blowing benefits of AM by improving the performance of existing applications and making it possible to produce new applications that were previously impossible.
Please contact us for additional information at www.elementum3d.com